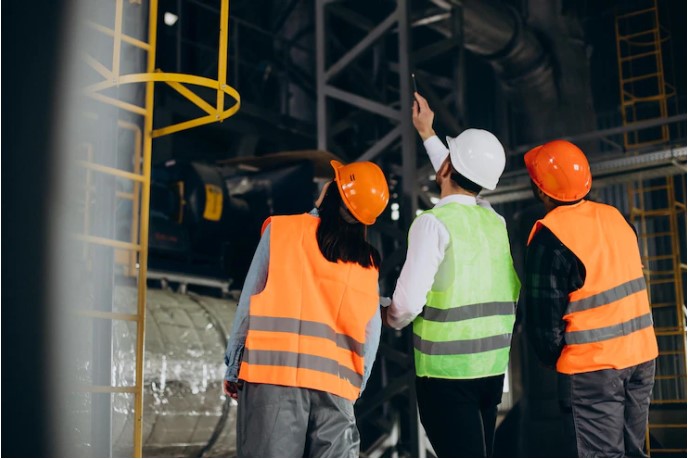
Safety and productivity are two sides of the same coin in industrial engineering. Both are essential for achieving optimal performance in a manufacturing or production setting. However, balancing both may be challenging. In this blog post, we will discuss five simple strategies for improving safety and productivity in industrial engineering.
As stated in this article by engineering company Bendtech, safety should always be the top priority in any industrial setting. A safe working environment not only protects the well-being of employees but also leads to increased productivity and overall efficiency.
Table of Contents
Here are five strategies for improving safety and productivity in industrial engineering
1. Implement proper training programs: Proper training is one of the most important strategies for ensuring the safety of employees in an industrial setting. It is essential for equipping employees with the knowledge and skills they need to identify and prevent potential hazards. For example, training employees on the proper use of equipment, the identification of potential hazards, and emergency procedures can significantly reduce the risk of accidents and injuries. Training employees on safety protocols and regulations can also help ensure compliance and avoid fines and penalties.
Proper training programs for industrial engineers are important for several reasons. They can help industrial engineers:
- Understand the latest industry standards and best practices for optimizing production processes and supply chain management.
- Develop the technical skills and knowledge needed to design, implement and monitor systems that increase efficiency and productivity.
- Learn how to use advanced tools and technologies, such as simulation software, to analyze and improve manufacturing processes.
- Understand the importance of safety and ergonomics in the workplace, and how to implement strategies to reduce accidents and injuries.
- Develop problem-solving and critical thinking skills that are essential for identifying and resolving issues in industrial operations.
- Enhance their ability to make data-driven decisions, by learning how to collect, analyze and interpret data to improve business performance.
- Be aware of the current trends and regulations that affect their industry and be better prepared to adapt to changes.
2. Utilize technology: Technology can play a critical role in enhancing safety and productivity in industrial engineering. One of the key ways in which technology can be used to improve safety and productivity is through automation. Automation can help reduce the risk of human error by automating repetitive and dangerous tasks. This can lead to increased safety as fewer employees are exposed to hazardous conditions. Additionally, automation can make processes more efficient by reducing the need for manual labor and increasing the speed and accuracy of tasks.
3. Encourage effective communication: Good communication is essential for promoting safety and productivity in an industrial setting. By encouraging open communication among employees, potential hazards can be identified and addressed more quickly. Additionally, effective communication can help improve collaboration and teamwork, leading to increased productivity.
Several advantages of good communication in industrial engineering:
- Improved productivity: Clear and effective communication can help to streamline processes and reduce confusion, which can lead to increased productivity and efficiency in industrial operations.
- Better decision-making: Good communication allows for the sharing and exchange of ideas and information, which can lead to more informed and effective decision-making.
- Enhanced team collaboration: Effective communication can help to build and maintain strong working relationships within teams, leading to better collaboration and problem-solving.
- Improved safety: Good communication can help to ensure that workers are aware of potential hazards and safety protocols, reducing the risk of accidents and injuries in the workplace.
- Reduced downtime: Clear and timely communication can help to identify and resolve problems quickly, reducing downtime and lost productivity.
4. Promote a safe and productive culture: A safe and productive culture is essential for achieving optimal performance in an industrial setting. By promoting a culture of safety and productivity, employees will be more motivated to work safely and efficiently. Additionally, a safe and productive culture can help attract and retain top talent.
5. Regularly evaluate and improve processes: Regularly evaluating and improving processes is essential for maintaining safety and productivity in an industrial setting. By identifying areas for improvement and making necessary changes, processes can be made safer and more efficient. Additionally, regular evaluations can help identify potential hazards and prevent accidents before they happen.
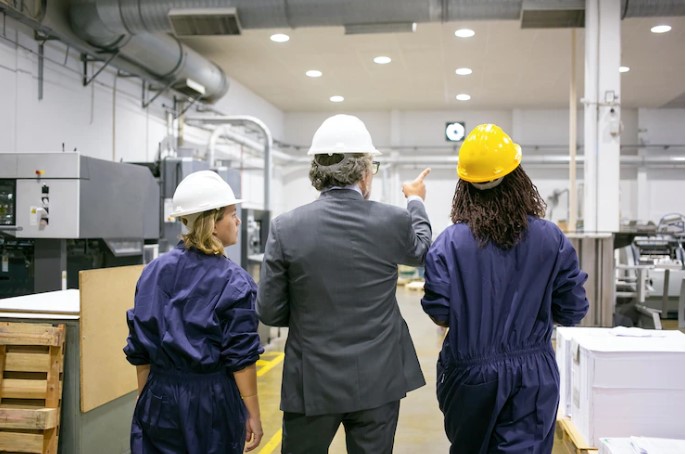
Some of the key benefits of regular process evaluation and improvement include:
- Increased efficiency: By regularly evaluating and improving processes, industrial engineers can identify and eliminate bottlenecks and inefficiencies in the production process. This can lead to increased productivity and reduced waste.
- Improved quality: Regular process evaluation and improvement can help identify and address quality issues, resulting in higher-quality products and fewer defects.
- Reduced costs: By identifying and eliminating inefficiencies and waste, regular process evaluation and improvement can help reduce costs associated with production.
- Increased competitiveness: Regular process evaluation and improvement can help companies stay competitive by keeping up with the latest industry trends and best practices.
- Compliance with regulations: Regular process evaluation and improvement can help companies ensure that they are in compliance with relevant regulations and standards, which can help avoid penalties or fines.